A manufacturer, whether it be watchmaker, active in medical or aerospace for example, do not consider a machine as an end in itself, but as a solution to reach its objectives. He is looking for a mean of production that perfectly fits its needs (present and sometimes future), provides an interesting return on investment, guarantees the required accuracy and quality while being trouble free. What a challenge for manufacturers of machines!
We met Mr. Guy Ballif, responsible for sales with Bumotec, a machines manufacturer who fully understands the complexity of the needs of its customers and that has developed its business accordingly. Mr. Ballif says: “We assure our customers that our promises will be kept and we sign on it”.

Bumotec is specialized in the realization of high-quality parts. Linear guides allow a never faulted precision which guarantees the production in high cadences. The parts are completed in one clamping from bars. Production is thus simplified and allows a better control of the process.
Innovation to the service of quality: linear guides The machines range includes quite a lot of innovations that allow Bumotec to push the boundaries further. The machines are equipped with linear motors to replace ball screws (traditionally a weak part in the industry of machines). Provided without mechanical element, the transmission of movement ensures very high precision and repeatability without fault. Thus small precise machining can be guaranteed (for example a diameter very accurately milled using interpolation). Another advantage of this technology is provided by the electromagnets ensuring movements; the frames being drawn onto each other with a great force the rigidity of the machine is thus significantly increased. Furthermore this driving concept requires no maintenance.
Innovation to the service of quality: spindles Tools considered as fixed, required for turning or even broaching operations are introduced into the spindle usually dedicated to so-called rotating tools. Turning operation with interrupted cut for example may generate important shocks onto the spindle and can badly influence the quality of hybrid bearings. To solve this problem, Bumotec has developed a system of "disengagement" of the spindle bearings in machining position. Thus, the potential shocks that may affect accuracy are dissipated into the cast iron sheath and not into the mechanism of the spindle and bearings. Product life, accuracy, quality and surface finishes are therefore preserved for a long time.
Innovation to the service of quality: thermal stabilization With cycle times reaching several dozen of minutes (depending on the part), manufacturers cannot afford to machine setting parts out of tolerance. Mr. Ballif said: “We have designed machines with integrated cooling at the level of the spindles, the linear motors and the B axis. The purpose is to ensure that the first part is already good and we reach it. We have made many measures that demonstrate a machine stability in the order of 2.5 micron on a full day of production; from as early as a few minutes after starting it".
To stick to the market: the application On the basis of a modular machine, Bumotec specialists build custom machines. The building on standard modular elements ensures quality and reliability. For example, the S191machine counter-operation system can be set up with a vice or a complete counter-spindle ensuring 5-axis machining or a combination of a rotating spindle and specific chucks... everything is possible to meet the needs.
You will be able to discover more about Bumotec’s machines in our next issue.
Bumotec SA Les Communs 1625 Sâles Switzerland Tel : +41 26 917 84 01 Fax : +41 26 917 81 18 [email protected] www.bumotec.ch
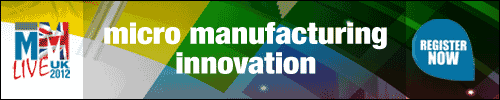