Black coatings have been very popular for some years in the field of watchmaking, but also eyeglass frames, leather goods, writing instruments and jewellery.
Few black coatings are made by electroplating (black chrome, black nickel, black gold, black rhodium ...) but the majority is made by dry and in particular by the DLC technique (Diamond Like Carbon).
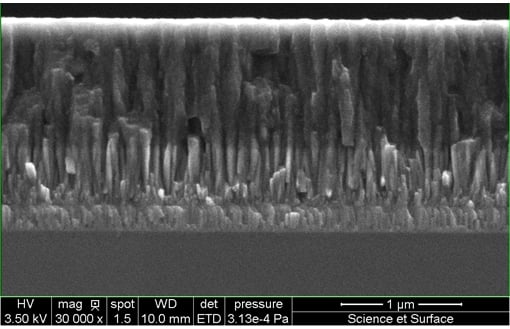
Progress on conducting coatings: The SEM photo shows that the developed coating has a fully columnar structure, which is confirmed by X-ray diffraction.
A significant proportion is produced by PVD (precisely by reactive magnetron sputtering). This technology has some advantages that not share DLC coatings. Let’s have a look at the PVD technique and its recent developments.
Let’s remember some DLC coatings facts
DLC coatings can be of type Ta: C (for Tetra-Amorphous-Carbon). They are obtained by sputtering (PVD) or by a cathodic arc. They are very hard but have very high internal stresses.
DLC coatings can also be of type a: C-H (for Amorphous-Carbon-Hydrogen). The hydrogenated fraction makes a little less hard coating, but in return, they are thicker and more resistant to corrosion.
They are generally obtained by the technology of PECVD using different precursors.
DLC coatings are being developed including diamond structures (called hybridization sp2 & sp3) in a graphite matrix (sp1 hybridization).
It is therefore, possible, to a certain extent, to vary the proportion of different hybrids and thus adapt the performance of the layer based on the use that we want to do.
TiAlN coatings, the Graal as black treatment?
After exploring a number of possibilities, the (small) environment of manufacturers of decorative PVD focused and developed black layer nitride-based of Titanium-Aluminium. Indeed, all the properties of this ceramic and the right balance of properties offered enabled this development. (We will enter into details of coatings considerations in a future issue of Eurotec)
A true technical advance
The decorative black PVD coatings based on the use of TiAlN obtained by sputtering represent really a technical advance. Why? Because these layers have no exceptional performance in a specific area, but represent a compromise that is quite interesting in most areas that are usually tested in the watch making industry; thus:
- This ceramic allows achieving a neutral black colour. Brightness is metallic and does not become "coal"; a L * of between 35 and 40. The other specular components a * (red-green) and b * (blue-yellow) are close to zero, so the colour is neutral.
- The colour is reproducible without any particular difficulty.
- The diffusion of the coating in 3D even in complex geometries is great.
- Wear resistance, abrasion resistance is very high.
- Hardness of the layer is high, so insensitive to scratches.
- Internal stresses are low, which ensures high adhesion.
- Corrosion resistance is high in virtually all standard areas.
- It is possible to strip chemically the layer to remake it later.
- It is possible to decline in interesting proportions fingerprint sensitivity caused by the columnar structure of the layer.
Although DLC coatings have taken a major boom in recent years, PVD technology continues to grow and now offers very attractive performance.
IONITEC SAS markets such type of long lasting PVD black layer for several months under the name PURE BLACK.
To know more, please contact:
SURFACES SYNERGIE HOLDING
Alexandre BEUQUE
Chargé d’Affaires
+33 (0)6 89 99 35 95
[email protected]
8, rue de la Batheuse
F. 25120 MAICHE
Tél. +33 (0)3 81 55 46 80
Fax +33 (0)3 81 55 46 84
www.surfaces-synergie.com
We will publish a whole article in a next issue of Eurotec on black PVD coatings.